
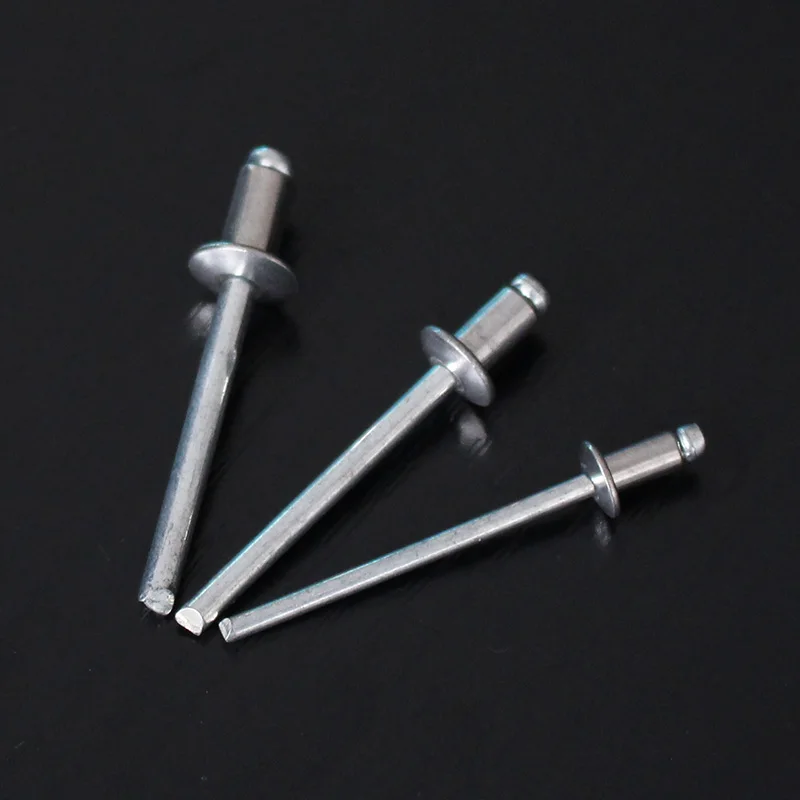
The dome head is considered standard, and is the most common head style and suitable for a very wide range of applications.They are a good choice if clearance is an issue because there are moving parts near the far side of the join.īlind rivets come in several head styles, but the three most common are the standard head, otherwise referred to as dome head, the countersunk head (usually abbreviated to the letters CSK), and the large flange head. When used, the multigrip blind rivet compacts down on the far side of the join, leaving less of the shaft sticking out. These are specifically designed for applications where the required length of the rivet is unknown. Less widely used by Mica customers are probably multigrip blind rivets.These four segments curl back on themselves, spreading the load over a wider area on the far side of the join. Peeled blind rivets have a rivet shaft that splits into four segments, rather like a peeled banana.Sealed blind rivets have a closed end and when used provide a waterproof attachment they are used in applications such as bakkie canopies – to attach hinges and other attachments to the fibreglass or aluminium canopy, and marine or boating applications, where it is important that assemblies be watertight.Standard rivets are the most common and used for such applications as securing security gate locks in their housing in the gate, but they are not watertight and not as strong as some other types of blind rivets.There are several common types of blind rivets each with its own features that suit it best to a particular task or range of tasks. If it is too large, the rivet might simply pull right through the hole. However, it is important that the hole drilled for any rivet is the correct diameter – that is, just large enough to accommodate the rivet. Pop rivets produce strong fastenings, they are resistant to vibration and tampering and when installed, neither the rivets nor the riveting tool mar the surfaces of the materials being joined.
#RIVET SIZES FREE#
(If the mandrel shaft does not fall out of its own accord, opening the riveter will push the end of the mandrel out of the socket, and a light tap with a hammer will free it.) The mandrel is pulled out the rivet and dropped out of the rivet gun, ready for the next rivet to be inserted. As the riveter is operated, the mandrel is placed under a great deal of strain and finally the head snaps off and the join is secure. This locks the rivet body very firmly against the surface of the material. As the mandrel is pulled through the rivet, its head increases the diameter of the rivet shaft, bulging it outwards. The mandrel has a head slightly larger than the mandrel’s diameter and the channel in which the mandrel is very snugly seated in the rivet body there is also a slightly narrower section of the mandrel just below the head so that it will break at that point. For the purposes of this feature we’re going to use the term ‘pop’.Īs you know, screws, bolts or nails are used in a very wide range of applications, but often riveting is the best option.Ī pop rivet comprises of the rivet itself (most usually aluminium) through which passes a tightly fitting steel mandrel – rather like a nail.


These rivets are also called blind rivets – this name being derived from the fact that they can be used when the operator cannot see the far side of whatever materials he or she is joining. So, here we are going to cover pop rivets (named for the sound they make when their mandrel snaps). Rivets are still widely used in aircraft and in household appliances – particularly in items such as refrigerators, stoves and ovens, microwaves and so on. Welding has now largely taken over in ship, bridge building, buildings and other fields. Rivets of many different types and materials have been used – and continue to be used – in a vast range of applications.įor instance, they have been used in ships, steel bridges, buildings, armoured fighting vehicles, machinery and more.
